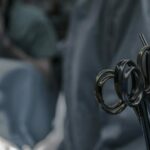
Logistique des hôpitaux : une filière exposée
15 octobre 2024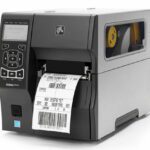
Guide de l’imprimante industrielle en entrepôt
29 octobre 2024Combien je stocke de palettes sur 1 000m2 ?
Cela dépend de pas mal de facteurs bien entendu : la hauteur de l’entrepôt, la typologie des racks choisis, le matériel de manutention sélectionné, la typologie des marchandises,, la largeur des allées, la disposition du bâtiment, etc….
La capacité de stockage d’un entrepôt demeure un facteur déterminant pour son efficacité opérationnelle et/ou son attractivité commerciale. Les 3PL en sont l’exemple parfait et optimisent chaque moyen de stockage.
Le choix du bon système de stockage impacte donc directement l’utilisation de l’espace, les coûts d’exploitation et la productivité des équipes. Face à une multitude de solutions de stockage disponibles, il est essentiel de comprendre les différences fondamentales entre le racking conventionnel et les autres systèmes, tels que le racking mobile, le stockage par accumulation ou encore les systèmes automatisés.
Nous ferons d’abord un rapide aperçu de ces grandes méthodes avant de détailler les racks conventionnels à travers quelques exemples très concrets et ainsi répondre à la question de combien de palettes je stocke dans 1 000m2.
Racking conventionnel : la solution standard
Le racking conventionnel (ou rayonnage à palettes standard) est sans doute la solution de stockage la plus courante dans les entrepôts. Il s’agit de structures fixes où les palettes sont stockées sur des étagères en plusieurs niveaux, accessibles via des chariots élévateurs.
Caractéristiques :
- Capacité de stockage : Moyenne à élevée, dépendant de la hauteur sous plafond et de l’optimisation de l’espace, notamment la largeur des allées.
- Accessibilité : Accès direct à chaque palette, ce qui facilite la gestion du stock, en mode FIFO par exemple.
- Flexibilité : Grande flexibilité pour différents types de produits et de charges, mais nécessite des allées larges pour la circulation des chariots. D’où l’importance de bien choisir ses chariots logistiques.
- Investissement : Faible coût d’installation comparé aux systèmes plus avancés et un délai de mise en œuvre plutôt réactif.
Limites :
- Utilisation de l’espace : Nécessité de conserver des allées entre les racks pour le passage des chariots, ce qui réduit la densité de stockage.
- Efficacité : Moins adapté aux environnements à haute rotation ou aux très grands volumes en raison des limitations d’espace au sol.
Racking mobile : l’art de maximiser l’espace
Le racking mobile est une solution similaire au racking conventionnel mais montée sur des bases mobiles qui se déplacent sur des rails. Cela permet de réduire le nombre d’allées nécessaires en ne laissant qu’une seule allée ouverte à la fois.
Caractéristiques :
- Capacité de stockage : Très élevée. En éliminant les allées fixes, le racking mobile peut augmenter la capacité de stockage de 80 % par rapport aux systèmes conventionnels. Il est couramment utilisé dans les entrepôts à température négative pour optimiser la production de froid.
- Accessibilité : Accès à chaque palette, mais une seule allée est disponible à la fois. Moins adapté aux environnements nécessitant des accès multiples rapides. A noter que plusieurs allées peuvent s’ouvrir en même temps. Cela aura un impact sur la capacité de stockage.
- Investissement : Coût plus élevé en raison des systèmes mécaniques et électriques requis pour déplacer les racks.
- Utilisation de l’espace : Optimisation maximale dans les entrepôts où l’espace est limité et où la hauteur n’est pas suffisante pour maximiser les niveaux de palettes.
Limites :
- Vitesse d’accès : Plus lent que le racking conventionnel car il faut déplacer les racks pour accéder aux produits (envrion 50 secondes pour ouvrir une allée complète). Un rigoureux travail d’adressage des marchandises s’impose. La méthode ABC peut-être une alliée quotidienne et le diagramme spaghetti un outil régulier.
- Complexité mécanique : Nécessite une maintenance plus exigeante pour éviter les pannes. Cela demande aussi une rigueur de nettoyage importante pour limiter les la multiplication des causes comme la formation de glace dans les entrepôts à températures négatives.
Stockage par accumulation : pour les grandes séries avec homogénéité des lots
Le stockage par accumulation, aussi appelé Drive-In ou Drive-Through, est conçu pour maximiser la densité de stockage en éliminant les allées entre les racks. Les chariots élévateurs pénètrent directement dans les structures pour charger ou décharger les palettes. Ce type de stockage est de plus en plus automatisable avec des systèmes de navettes ou shuttles qui se déplacent au milieu de la structure.
Caractéristiques :
- Capacité de stockage : Très élevée. Idéal pour le stockage en grande quantité de produits identiques ou à faible rotation.
- Accessibilité : Accès en profondeur, donc la gestion des stocks est généralement en mode LIFO, ce qui le rend moins adapté aux produits périssables nécessitant un FIFO.
- Investissement : Coût modéré mais nécessite des chariots spécialisés et un agencement précis des racks. Quand il s’agit d’équiper avec des navettes ou shuttles, cette caractéristique est clairement impactée.
- Utilisation de l’espace : Maximisation de la densité de stockage horizontal et vertical.
Limites :
- Gestion des stocks : Accès limité à certaines palettes, ce qui complique la gestion de produits variés. 1 référence = travers complète.
- Sécurité : Plus de risques d’accidents liés à la manipulation des chariots à l’intérieur des racks.
- Taux de remplissage : possiblement faible
Opportunités :
Ce type de stockage par accumulation peut cependant être équipé d’un système de navette ou shuttle. Le recours à ces supports de manutentions autonomes dans la structure du rack présente plusieurs avantages parmi lesquels nous retrouvons ;
- Le fait de plus rentrer dans le rayonnage avec le chariot. Cela diminue considérablement le risque d’accident et celui de dégradation de la structure
- Une amélioration du taux de remplissage par un stockage mieux ordonné. 1 référence = 1 profondeur
Systèmes automatisés : la révolution de la logistique
Les systèmes de stockage automatisés (AS/RS, Automated Storage and Retrieval Systems) permettent d’optimiser l’espace et de réduire les coûts de main-d’œuvre grâce à des solutions robotisées.
Caractéristiques :
- Capacité de stockage : Très élevée. Ces systèmes utilisent la hauteur maximale disponible et minimisent les espaces inutilisés.
- Accessibilité : Accès rapide et automatisé à chaque article, parfait pour des environnements à haute rotation ou une grande variété de produits.
- Investissement : Coût initial très élevé, mais compensé par une réduction des coûts de main-d’œuvre à long terme ou une optimisation du coût d’exploitation logistique facturé par son prestataire logistique.
- Utilisation de l’espace : Optimisation maximale de la hauteur et des surfaces au sol grâce à la robotique.
- Flexibilité : accès direct aux marchandises préservé
- Inter-opérabilité requise avec le logiciel WMS de l’entrepôt
Limites :
- Dépendance technologique : Les systèmes nécessitent une maintenance régulière et des mises à jour pour éviter les temps d’arrêt.
- Exigence volumétrique : requiert une stabilité dans les volumes traités pour amortir l’investissement et servir la productivité des volumes
- Délais de mise en œuvre : il est courant de rencontrer une durée de 16 à 18 mois entre le contrat et les premières palettes stockées. Période moyenne à laquelle il faut ajouter l’avant-vente, les études de flux préalables et la maturité de la décision.
Focus sur la capacité des racks conventionnels
Maintenant que nous avons effectué ce travail préliminaire, concentrons nous sur le racking conventionnel.
Au travers de notre question centrale, nous allons visualiser les impacts sur la capacité, uniquement en changeant la donnée du matériel choisi :
Bâtiment (m2) | Type de chariot | Sol + Niveaux | Capacité palettes |
1 000 | Chariot rétractable sol | Sol +3 | 1 550 |
1 000 | Chariot gerbeur | Sol +3 | 1 650 |
<>1 000 | Chariot frontal | Sol +3 | 1 300 |
Intéressant, n’est ce pas ?
Il est important de rappeler que ces chiffres sont partagés à titre indicatif pour permettre une approche rapide et macro du sujet.
Ils ne remplacent en rien une étude produite par des professionnels du racking (MECALUX, Bluerack, Stow) qui prendra finement en compte les multiples éléments de solidité de la dalle, dimensions réelles du bâtiment ou encore les chariots utilisés et les typologies de flux de marchandises.
Enfin, pour les chariots, il est aussi très important de rappeler que seul un fabriquant de chariot pourra connaître et précisément donner la largeur des allées pour le type de chariot sélectionné qui, rappelons le, varie aussi selon la palette et les niveaux de gerbage.
Dans l’article présent, nous avons travaillé avec les dimensions indicatives ci-après : gerbeur : 2500 mm / frontal 3 roues : 3500 mm / rétract : 3000 mm. Et afin de donner un aperçu plus complet, voici un tableau de capacité théorique pour une surface de 3 000m2 avec une variation de hauteur.
Le gerbeur n’y figure pas considérant la pénibilité du travail des opérateurs trop importante pour que la capacité soit pertinente à partager.
Bâtiment (m2) | Type de chariot | Sol + Niveaux | Capacité palettes |
3 000 | Chariot rétractable sol | Sol +5 | 6 450 |
3 000 | Chariot rétractable sol | Sol +4 | 5 350 |
3 000 | Chariot rétractable sol | Sol +3 | 4 250 |
3 000 | Chariot frontal | Sol +3 | 3 650 |
A noter que le ratio de 1 pour 3 concernant les surfaces n’est pas applicable pour la capacité. Nous sommes ici sur un coefficient de 1.75.
Une collaboration Matthias & Pierre