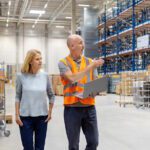
APS : l’outil indispensable à la supply chain
4 octobre 2023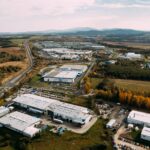
Pénurie d’offres foncières pour les logisticiens : un problème croissant
10 octobre 2023Dans le monde complexe de la logistique, l’efficacité est essentielle. Les erreurs lors de la préparation de commandes, communément appelées erreurs de picking ou de prélèvements peuvent avoir des conséquences graves sur la logistique d’une entreprise. Les coûts engendrés par ses erreurs varient en fonction de leur nature, de la taille de l’entreprise et du secteur d’activité.
Qu’il s’agisse du mauvais article prélevé ou de plusieurs commandes mélangées (mais si), ces erreurs sont coûteuses et nuisent à la satisfaction du client final. Cependant, avec l’automatisation des process, la formation appropriée du personnel et l’utilisation de systèmes de gestion des stocks, il est possible de les réduire considérablement.
L’impact financier des erreurs de picking n’est pas négligeable !
Les erreurs de picking sont plus que de simples malentendus en entrepôt. Elles ont un impact financier significatif sur les entreprises. Selon certaines études, le coût moyen d’une erreur de picking est estimé à près de 20 euros par commande. Ce chiffre peut sembler modeste, mais, point n’est besoin de sortir sa calculette, car cela s’additionne rapidement lorsque des milliers de commandes sont traitées quotidiennement.
Les coûts liés aux erreurs de picking sont multiples :
- Coûts de retour : Lorsqu’un client reçoit un article incorrect ou endommagé, il retourne généralement le produit à l’entreprise. Les coûts de traitement des retours, y compris les frais de transport, la main-d’œuvre et la réexpédition, peuvent être élevés, sans parler de l’empreinte carbone de l’erreur.
- Perte de clients : Les erreurs de picking peuvent entraîner la perte de clients. Les clients insatisfaits sont moins susceptibles de revenir pour d’autres achats et peuvent partager leurs expériences négatives avec d’autres, nuisant ainsi à la réputation de l’entreprise.
- Coûts de main-d’œuvre : Lorsqu’une erreur de picking est détectée, elle nécessite souvent l’intervention de la main-d’œuvre pour résoudre le problème. Cela inclut la recherche de l’article correct, son emballage et son expédition, ce qui peut représenter une charge de travail supplémentaire et coûteuse.
- Frais de stockage : Les erreurs de picking peuvent également entraîner des coûts de stockage supplémentaires, car les articles retournés doivent être stockés jusqu’à leur réexpédition.
Quelles solutions mettre en œuvre pour minimiser ces erreurs?
Comment les entreprises peuvent-elles minimiser ces erreurs coûteuses de picking en entrepôts ? Certes, il n’y a pas de recette magique, mais il apparait que la réponse réside dans la maturité, l’automatisation et l’amélioration des processus de gestion des stocks.
Les pistes de l’automatisation et de la formation
L’automatisation est la clé pour réduire le taux d’erreur lors de la préparation de commandes, quand les produits peuvent s’y prêter. Les systèmes de picking automatisés utilisent des robots ou des systèmes de convoyeurs pour collecter les articles, éliminant ainsi l’erreur humaine, qui existera toujours quelque soit le degré d’implication du personnel. Mais à ce titre, a t-il reçu la formation adéquate ? car elle est essentielle. Les employés doivent comprendre l’importance de la précision dans la préparation des commandes et être familiarisés avec les systèmes et les processus de l’entrepôt.
Un taux de conformité picking inférieur à 99,5% est clairement une urgence à traiter et un risque saillant pour l’entreprise.
L’automatisation des processus de préparation de commandes, tels que l’utilisation de robots ou de systèmes de convoyeurs automatisés, réduit évidemment le risque d’erreur humaine. Ces systèmes automatisés peuvent collecter des articles avec une grande précision, garantissant que les bons articles sont collectés dans les bonnes quantités. Ils peuvent par ailleurs, collecter des articles beaucoup plus rapidement que les opérateurs humains. Cela permet d’augmenter le nombre de commandes préparées par heure, ce qui améliore l’efficacité de l’entrepôt.
Moins d’erreurs donc moins de coûts liés aux retours de marchandises, à la réexpédition, aux remboursements aux clients insatisfaits, et aux pertes de ventes. Cela se traduit par des économies financières significatives.
Un autre point d’amélioration réside dans l’utilisation de systèmes de gestion des stocks. Les WMS permettent de suivre et de gérer efficacement les stocks. Ils peuvent aider à identifier les articles mal placés, à suivre les niveaux de stock en temps réel et à réduire les risques d’erreurs.
Et encore ?
- Mettez en place des vérifications croisées pour chaque commande préparée. Un deuxième employé peut vérifier que les articles sélectionnés correspondent à la commande avant l’expédition.
- Analysez les erreurs de picking pour identifier les tendances. Cela peut révéler des problèmes récurrents qui peuvent être résolus grâce à des ajustements de processus ou de formation. Cet axe est trop souvent négligé alors que pourvoyeurs de réponses et de plan d’actions efficaces ensuite.
- Encouragez les clients à signaler les erreurs de commande. Leurs retours peuvent être une source précieuse d’informations pour améliorer les processus.
Les erreurs de picking en entrepôts peuvent avoir un impact financier significatif sur les entreprises. Cependant, avec l’automatisation, la formation appropriée du personnel et l’utilisation de systèmes de gestion des stocks, il est possible de réduire considérablement ces erreurs coûteuses. En investissant dans des processus de préparation de commandes plus précis, les entreprises peuvent améliorer leur efficacité opérationnelle et offrir une meilleure expérience client, tout en économisant de l’argent sur le long terme.
Et ne JAMAIS sous estimer la valeur ajoutée de l’analyse des stocks et des erreurs picking.
Elle demeure l’antichambre de la promesse client tenue et de la performance économique durable.