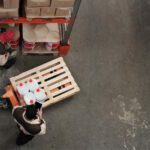
La manutention d’hier, d’aujourd’hui et de demain
14 novembre 2023
ID Logistics confie son hébergement IBM Power à ACSEP
16 novembre 2023L’efficacité opérationnelle est au cœur de tout business pérenne, et la gestion de la production est un élément clef de cette dynamique. Face à des marchés en constante évolution et à des demandes de plus en plus variées, les entreprises sont confrontées à des choix stratégiques quant à la manière dont elles organisent leur processus de fabrication.
Il existe quatre principales stratégies de production qui représentent des approches distinctes, chacune ayant des implications significatives sur des aspects essentiels tels que le niveau de stock, le délai de livraison, et la personnalisation des produits par exemple. Il est important de les identifier pour les mettre en place, les analyser et les faire performer au quotidien.
MAKE TO STOCK – fabrication sur stock
- Stock : Niveau de stock élevé pour répondre rapidement à la demande.
- Délai de livraison : Généralement plus court car les produits sont déjà fabriqués.
- Coûts : Peut entraîner des coûts de stockage élevés, mais permet des économies d’échelle dans la production.
Stratégie qui s’adapte bien à de grandes séries mais nécessite l’utilisation d’outils de prévisions de la demande ou DDMRP pour finement piloter cette stratégie.
ASSEMBLE TO ORDER – assemblage à la commande
- Stock : Stock de composants préfabriqués, mais l’assemblage final se fait à la commande.
- Délai de livraison : Plus court que le make to order car certains composants sont déjà produits.
- Coûts : Réduit les coûts de stockage par rapport à la fabrication sur stock, avec des coûts de production plus modérés.
Choix stratégique qui demande une gestion fine entre les composants préfabriqués qu’il faut en quantité suffisante et l’organisation adaptée pour mettre en oeuvre l’assemblage final pour livrer les clients. Cette stratégie nécessite aussi l’adjonction d’outils dédiés Supply Chain.
MAKE TO ORDER – fabrication à la commande
- Stock : Niveau de stock plus bas car les produits ne sont fabriqués qu’en réponse aux commandes.
- Délai de livraison : Peut être plus long en raison du processus de production déclenché par une commande.
- Coûts : Moins de coûts de stockage, mais des coûts de production unitaires peuvent être plus élevés.
Cette stratégie donne la part belle à la personnalisation du besoin client. Elle implique généralement une nomenclature claire et disponible des matières premières et composants pour réaliser la production dans le meilleur délai pour le client. Un outil de Business Process Management est recommandé pour garder la main sur le process de production.
ENGINE TO ORDER – design à la commande
- Stock : Niveau de stock bas, avec la conception et la fabrication déclenchées par une commande.
- Délai de livraison : Peut être le plus long en raison de l’étude préalable nécessaire.
- Coûts : Généralement les coûts les plus élevés en raison de la personnalisation et de la complexité de la conception.
Cette stratégie requiert l’utilisation d’un bureau d’études pour la phase de conception avant de lancer la production. Elle se rencontre dans la sous-traitance industrielle ou la production de pièces spécifiques. Un solide outil de BPM voir même de gestion de projet ne sera pas superflu pour servir efficacement le client avec ce type de stratégie.
Ces termes reflètent différentes approches dans la gestion de la production, allant de la fabrication en anticipation basée sur des prévisions à la personnalisation complète en réponse aux spécifications du client. Le choix de la stratégie dépend bien entendu des objectifs de l’entreprise, du type de produit, de la variabilité de la demande, et de la nécessité de personnalisation.
A noter que ces stratégies peuvent être combinées dans une même entreprise pour proposer une Supply Chain complète et surtout adapté aux besoins des clients du marché administré.