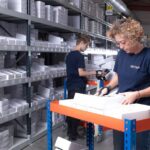
Avec le WMS IzyPro, Octika gère sa logistique les yeux fermés
23 janvier 2024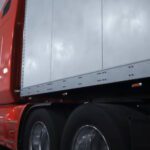
L’arrivée des moteurs électriques dans le transport routier
6 février 2024Un plan de masse, une boite de feutres de couleurs, des chaussures de sécurité au pied et c’est parti !
Diagramme spaghetti & Visualisation de flux physiques
Le diagramme spaghetti est un outil de visualisation des flux physiques, qu’ils soient de produits, de personnes ou d’informations. Il tire en effet son nom de sa ressemblance avec un plat de spaghettis, car les flux se présentent souvent de manière complexe et entremêlée lors de la 1ère représentation. Il est important de souligner que la représentation du flux dans un format très visuel et coloré facilite grandement la compréhension et aide considérablement à conscientiser la situation pour en tirer les conclusions qui s’imposent.
Méthode de travail
Le diagramme spaghetti est réalisé à l’aide d’un plan ou d’une maquette de l’espace étudié. Les flux sont ensuite tracés à l’aide de lignes colorées, en indiquant leur sens et leur intensité (fréquence, répétition par exemple). Il est important de prendre en compte tous les flux, y compris les plus petits même ceux perçus comme insignifiants. Le diagramme spaghetti a été développé par Taiichi Ohno, un ingénieur japonais qui est considéré comme le père du Lean Manufacturing.
Le diagramme spaghetti est un des nombreux outils clefs du LEAN management, qui vise à améliorer l’efficacité des processus industriels de façon continue.
Pourquoi utiliser un diagramme spaghetti ?
Parce qu’il est d’abord très simple d’utilisation et de mise en oeuvre. Ce qui fait du diagramme spaghetti un outil précieux pour la logistique qui permet notamment de :
Améliorer la visibilité des flux physiques :
Le diagramme spaghetti permet de rendre compte de manière claire et concise les flux qui traversent un espace donné. Cela permet de mieux comprendre comment les choses fonctionnent et d’identifier les potentiels dysfonctionnements comme des goulots, congestions ou saturation d’espaces.
Identifier les inefficacités :
Le diagramme spaghetti permet de facilement visualiser les inefficacités des flux physiques, telles que les croisements inutiles, les déplacements excessifs ou les attentes. Ces inefficacités peuvent être source de coûts, de perte de temps et de productivité.
Améliorer l’efficacité des flux :
Enfin, il doit être utilisé pour identifier des pistes d’amélioration de l’efficacité des flux physiques. Ces améliorations possibles, mises en évidences par la représentation visuelle, peuvent concerner l’aménagement de l’espace, l’organisation du travail ou les processus. D’aspect simple de prime abord, le diagramme spaghetti reste un puissant outil d’observation terrain et d’amélioration continue. Il est un excellent moyen d’augmenter l’efficacité des flux physiques et de réduire les coûts et les pertes.
C’est aussi une belle opportunité de valoriser des collaborateurs en leur confiant cette méthode facile d’acquisition pour amplifier les performances d’un périmètre de travail.
Quelques exemples d’application du diagramme spaghetti :
- Les entrepôts : Cela peut concerner l’aménagement des allées, l’emplacement des racks ou la gestion des flux de picking. A coupler idéalement avec un travail d’analyse ABC.
- Une zone de co-packing ou de kitting : ces zones de travail sont de plus en plus plébiscités par les donneurs d’ordre et clients pour différencier un produit au dernier moment ou juste avant l’expédition. Le digramme spaghetti se révèle un allié de poids pour éclairer ces zones de travail parfois organisées “à l’arrache” pour répondre à l’urgence de la demande.
- Les usines et ateliers de production : L’approvisionnement des bords de ligne est un sujet tout à faire propice à l’utilisation de cette méthode.
Pour la recette, c’est par ici :
Définir le périmètre d’étude
La première étape consiste à définir le périmètre d’étude du diagramme spaghetti. Cela signifie identifier l’espace ou le processus que l’on souhaite visualiser. Par exemple, on peut vouloir réaliser un diagramme spaghetti de l’ensemble d’un entrepôt, d’une ligne de production ou d’un processus de préparation de commandes. Se mettre d’accord sur le périmètre d’étude, c’est la base.
Collecter les données, comprendre l’enchainement des étapes dans le périmètre d’étude
Une fois le périmètre d’étude défini, il faut collecter les données nécessaires à la réalisation du diagramme. Cela doit inclure le support comme un plan ou une maquatte, des relevés de distances, des gammes opératoires et bien entendu des observations directes. C’est la partie centrale de cette méthode et elle doit obligatoirement se dérouler sur le terrain pour tout ou partie de cette étape. Plus vous collecterez de données, plus votre diagramme sera précis.
Tracer les flux
L’étape suivante consiste à tracer les flux physiques sur le support retenu. Bien souvent un plan de masse fait parfaitement le job. Tracez tous les flux comme écrit précédemment, cela vous aidera à distinguer les flux et identifier les dysfonctionnements. C’est ici que la trousse de feutres de couleur est à ouvrir !
Analyser les résultats
Une fois les flux tracés, il faut les analyser pour identifier les inefficacités. Cela peut inclure la recherche de croisements inutiles, de déplacements excessifs ou d’attentes. C’est un travail à mener seul ou de façon collaborative. La représentation visuelle de l’étape 3 facilitera le travail en groupe et offrira une base de travail commune. Efficacité garantie.
Proposer des améliorations
L’étape finale consiste à proposer des améliorations des flux physiques pour obtenir des résultats. A ce stade de la méthode, il est important de planifier un suivi pour ne pas laisser ce travail sans mesure à postériori. C’est le moment de collecter les fruits du travail engagé.
Cette méthode d’analyse des flux s’adapte à une grande variété de contextes.
Pour aller plus loin :
- Liker, J. K. (2004). The Toyota Way: 14 Management Principles from the World’s Greatest Manufacturer. McGraw-Hill Education.
Ce livre aborde les principes fondamentaux de la production allégée (lean manufacturing), dont les diagrammes spaghetti sont un outil clé pour identifier les inefficacités dans les flux de travail. - Rother, M., & Shook, J. (2003). Learning to See: Value Stream Mapping to Add Value and Eliminate Muda. Lean Enterprise Institute.
Bien que ce livre soit principalement axé sur la cartographie de la chaîne de valeur (Value Stream Mapping), il explore également l’importance des diagrammes spaghetti dans l’optimisation des flux de travail. - Dennis, P. (2007). Lean Production Simplified: A Plain-Language Guide to the World’s Most Powerful Production System. Productivity Press.
Un guide pratique sur la production lean, qui explique de manière simple comment les outils tels que les diagrammes spaghetti peuvent être utilisés pour améliorer les flux de production.