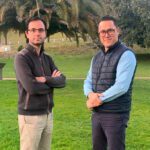
Cartoway : un logiciel innovant d’organisation de tournées
23 février 2024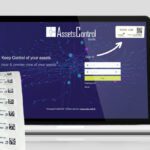
Actidel et inotec : Une Collaboration Fructueuse pour la Gestion Avancée des Actifs par RFID
1 mars 2024L’automatisation des entrepôts est en train de révolutionner le secteur logistique à une vitesse fulgurante. Jadis, la maintenance était principalement cantonnée au monde de production industrielle, mais aujourd’hui, avec la montée en puissance des technologies robotiques dans les entrepôts, le paysage de la maintenance logistique évolue de manière significative et rapide. L’essor et le succès de la licorne française EXOTEC témoigne de cette tendance lourde du métier logistique.
La maintenance devient donc une compétence clef indispensable dans un entrepôt pour assurer l’exécution conforme et permanente des opérations.
Cette transformation exige une adaptation rapide des compétences et une compréhension approfondie des différents niveaux de maintenance.
Blogistics propose d’éclairer ce sujet, de plus en plus logistique, en mettant en lumière les différents type de maintenance et les différents niveaux de maintenance comme définis par l’AFNOR (Association Française de Normalisation) dans la norme NF-X 60 000.
Les avantages de la robotisation en entrepôt sont nombreux.
Les robots peuvent en effet effectuer des tâches répétitives à grande vitesse et avec une précision accrue. Les systèmes automatisés optimisent les flux de marchandises et réduisent les temps de traitement. Les robots soulagent également les opérateurs des tâches physiques les plus lourdes, répétitives, distantes ou dangereuses. Ils permettent en outre de limiter les troubles musculo-squelettiques et d’améliorer les conditions de travail pour un certain nombre de tâches. Enfin, les systèmes automatisés collectent et analysent des données en temps réel ce qui permet d’assurer une meilleure traçabilité des produits et de prévenir les erreurs.
Seulement voilà, cela crée de nouveaux défis et notamment en termes de maintenance. Les profils “classiques” de la maintenance logistique doivent désormais être formés pour entretenir et réparer non seulement des machines traditionnelles, mais aussi des systèmes robotiques complexes.
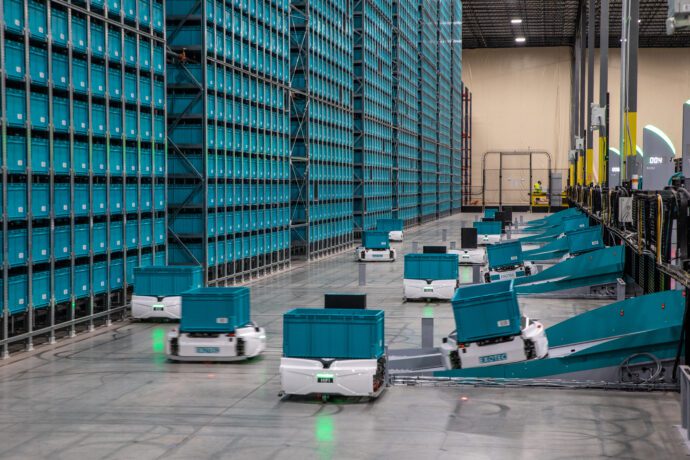
(c)EXOTEC
Les différents types de maintenance
La maintenance corrective : qui intervient après la détection du dysfonctionnement
Il s’agit dans ce cas de dépanner (maintenance palliative) ou de réparer (maintenance curative).
Pour intervenir, il est nécessaire de connaître le fonctionnement des équipements et d’avoir sur places les outils nécessaires à la réalisation de l’opération de maintenance. Cela peut notamment prendre la forme de manuels d’instructions ou de procédures de dépannage par exemple.
La maintenance préventive : qui intervient avant la détection du dysfonctionnement
Ce type de maintenance peut prendre 3 formes différentes.
- La maintenance préventive systématique dont l’objectif est de prévenir les pannes par des contrôles planifiés à intervalles réguliers.
Ce niveau de maintenance implique des actions planifiées visant à réduire la probabilité de défaillance ou la détérioration d’un équipement par un contrôle planifié. Dans un entrepôt automatisé, cela peut inclure des vérifications régulières des robots, des systèmes de convoyage et des logiciels de contrôle pour détecter et résoudre les problèmes potentiels avant qu’ils ne deviennent critiques. Elle se caractérise par un planning défini à l’avance et un rigoureux suivi des réalisations. - La maintenance préventive conditionnelle dont le principal but est de surveiller l’état des équipements pour déclencher des interventions ciblées. Ce niveau de maintenance implique la surveillance continue des conditions de fonctionnement des équipements à l’aide de capteurs et d’instruments spécifiques. Dans un entrepôt automatisé, la maintenance conditionnelle peut être utilisée pour surveiller la température, la vibration ou d’autres paramètres critiques des machines afin de détecter les signes de défaillance imminente.
- La maintenance préventive prédictive dont l’enjeu est d’anticiper les pannes grâce à l’analyse de données et l’intelligence artificielle.
Ce niveau de maintenance repose sur l’utilisation de technologies avancées telles que les capteurs IoT et l’analyse de données pour prédire les défaillances potentielles et planifier les interventions de maintenance de manière proactive. Dans un entrepôt automatisé, la maintenance prédictive peut aider à estimer la durée de vie des batteries des robots pour optimiser leur remplacement en fonction de l’usage et des conditions d’utilisation par exemple.
Les différents niveaux de complexité de maintenance
Selon l’AFNOR précédemment cité dans l’article, il existe 5 niveaux de maintenance où chaque niveau correspond au degré de complexité de l’opération de maintenance à prévoir. Cela permet notamment de cibler le niveau d’expertise requis pour la réaliser, mais aussi de l’importance des moyens à mettre en œuvre (outillage, espace physique à prévoir…). Cette classification permet aussi de juger si une action peut être plutôt faite en interne ou si elle nécessite l’intervention de prestataires externes qualifiés.
Niveau 1 : Maintenance simple
Il s’agit d’opérations de réglages simples ne nécessitant pas de démontage.
Réalisables par l’exploitant ou un opérateur non spécialisé. Ce niveau de maintenance est une opportunité de responsabiliser les opérateurs et les amener à réaliser d’autres tâches logistiques.
Exemples : relevé d’un compteur, remplacement d’une ampoule.
Niveau 2 : Maintenance peu complexe
Ce niveau concerne les actions de maintenance préventive ou de dépannage suivant une procédure simple.
Remplacement de pièces sans démontage global de l’équipement. Elles sont réalisables par un technicien qualifié et présentent également une solide opportunité de faire évoluer des collaborateurs sur un contenu de poste différent et correspondant à l’évolution du métier.
Exemples : vérification de capteurs, remplacement d’une courroie.
Niveau 3 : Maintenance complexe
Ici sont concernées les interventions sur des équipements complexes après diagnostic et identification du problème.
La prise en compte du fonctionnement global de l’appareil est requise à compter de ce niveau de complexité. Les actions sont réalisables par des techniciens spécialisés avec un outillage précis et une formation adéquate.
Exemples : vérification de combustion d’une chaudière, changement d’une pompe.
Niveau 4 : Maintenance de grande importance
Ce sont des travaux de maintenance corrective et préventive, hors rénovation ou reconstruction. Cela nécessite une expertise particulière et une supervision par un responsable spécialisé. Ce niveau de maintenance requiert que les actions soient réalisées avec un outillage et une documentation spécifiques. Les interventions sont souvent réalisées dans un atelier pour disposer de tous les moyens nécessaires à la réussite du travail de maintenance.
Exemples : analyse de vibration, révision d’une pompe.
Niveau 5 : Maintenance d’opérations complexes
Opérations généralement confiées au constructeur ou à des prestataires externes dans le cadre de l’application d’une nouvelle règlementation ou d’une réparation demandant la considération générale et totale de l’appareil concerné.
Exemples : mise en conformité d’un appareil, reconstruction ou réparation d’un appareil.
La fiche volante, réalisée par Hugo DUC, ci-dessous présente de façon synthétique ces 5 niveaux de complexité de la maintenance :
L’automatisation croissante des entrepôts représente donc une opportunité majeure pour accroître l’efficacité opérationnelle et améliorer la productivité dans le secteur logistique. Cependant, cela nécessite également une évolution des métiers de la maintenance pour répondre aux nouveaux défis posés par les systèmes automatisés. En intégrant ces grands principes de types et niveaux de maintenance définis par l’AFNOR, les responsables d’exploitation ont la possibilité (et le devoir) de positionner cette montée en compétence au cœur de leurs entrepôts et de leur management.
Dans un métier où les tâches logistiques exposent les opérateurs à d’importants risques de troubles MS, la montée en compétence sur des niveaux de maintenance 1 ou 2 est un levier d’évolution précieux pour diversifier le travail et assurer la résilience de l’appareil de logistique.